How to Extend the Lifespan of Your Industrial Cooling System
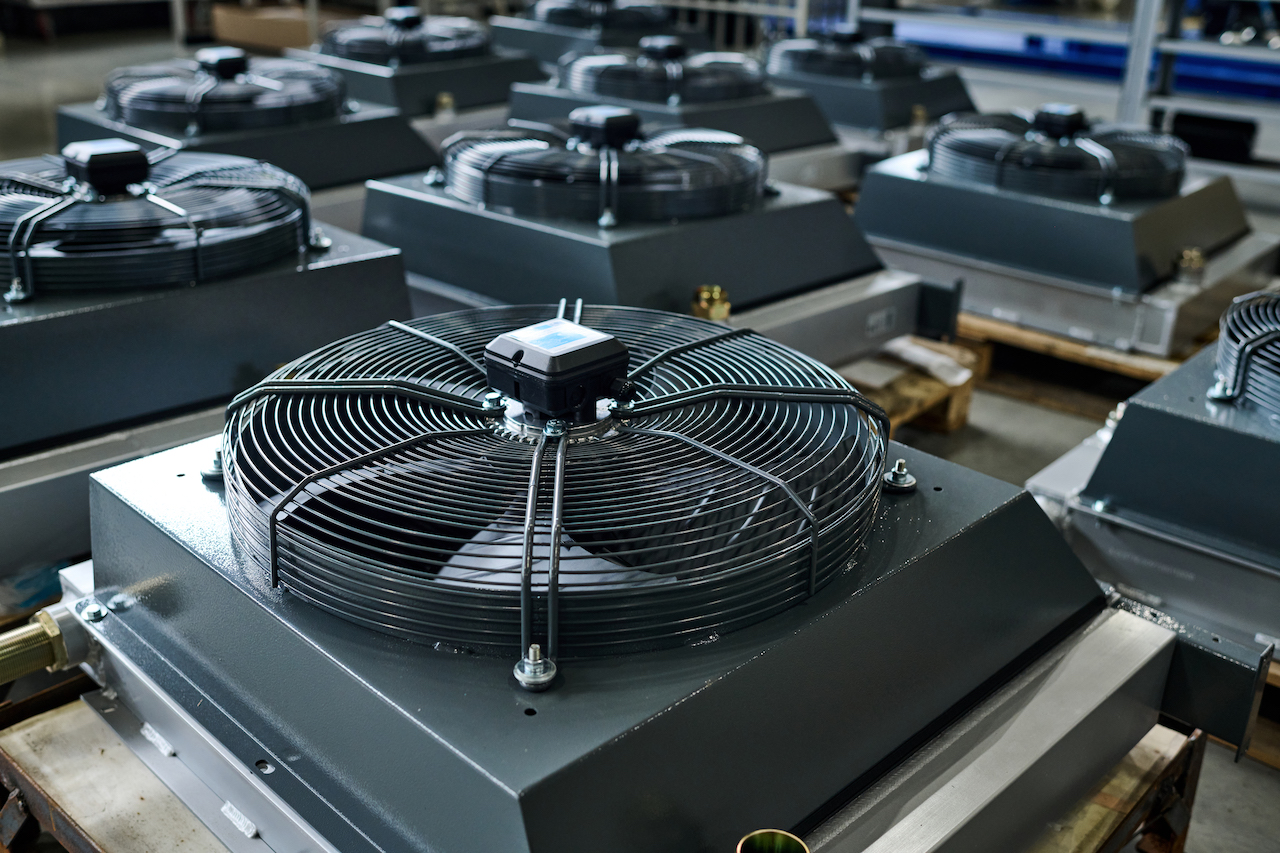
Industrial cooling systems are critical in maintaining operational efficiency across various industries. Whether you’re cooling equipment, managing process heat, or maintaining ideal storage temperatures, ensuring your cooling system’s longevity is essential to reduce downtime and increase cost-effectiveness.
One of the most commonly used systems in industries today is the industrial air-cooled chiller. These systems are favored for their efficiency, versatility, and minimal water usage, making them an excellent choice for various applications. Let’s explore how you can extend the lifespan of your industrial cooling system—especially your air-cooled chiller.
Benefits of Prolonging Your Cooling System’s Life
Before we get into the “how,” it’s worth understanding why extending the lifespan of your industrial cooling system matters:
- Reduced Costs: Less frequent replacement and repairs mean significantly lower expenses over the long term.
- Improved Efficiency: A well-maintained cooling system operates at optimal efficiency, saving energy and improving productivity.
- Minimized Downtime: Proper care reduces unexpected breakdowns, keeping your operations running smoothly.
Now, onto the actionable steps.
1. Schedule Regular Maintenance
Regular maintenance is the cornerstone of extending the life of any industrial equipment, including cooling systems. Keep a preventive maintenance schedule to address minor issues before they escalate.
- Inspect and clean components regularly. Dust, dirt, and debris can build up on components such as fins and condensers, especially in air-cooled systems that are exposed to the environment.
- Check for leaks. Refrigerant leaks not only reduce efficiency but can also lead to significant system damage if not addressed in time.
- Professional inspections. Have qualified technicians assess your system periodically to identify potential problems that might not be obvious.
2. Optimize Airflow for Air-Cooled Chillers
Air-cooled chillers rely on proper airflow for efficient cooling. Poor airflow can strain the system, leading to overheating and wear. Ensure the system is placed in a location with:
- Unobstructed airflow around the equipment.
- At least 24 inches of clearance from walls or other objects.
- No sources of hot exhaust or corrosive vapors nearby.
Regularly clean and inspect air filters, fans, and louvers to remove any dirt or blockages that might impede airflow.
3. Monitor Water and Refrigerant Quality
While air-cooled chillers don’t rely on water circulation like water-cooled systems, they still use refrigerant extensively. Regularly monitor refrigerant levels and ensure the quality of the system’s working fluid remains optimal. Contaminants in the refrigerant can damage critical components like coils and compressors.
Also, keep an eye on oil levels (if applicable) in your system, as proper lubrication reduces friction and wear.
4. Calibrate the System for Proper Load
Overloading your cooling system can accelerate wear and tear. Make sure the system is calibrated to handle the operational loads for your specific application. If you notice that your air-cooled chiller is frequently running at max capacity, it might be time to upgrade to a higher-capacity system or reduce the process heat loads.
5. Protect Against Environmental Elements
Air-cooled chillers are often exposed to outdoor environments. Protecting your system from harsh weather conditions can prevent unnecessary damage. Consider:
- Installing weatherproof covers or shelters without blocking airflow.
- Ensuring the unit is protected from excessive moisture, which can lead to corrosion of components.
- Applying anti-corrosion coatings for chillers installed near coastal or industrial areas with high humidity or pollution.
Final Thoughts
Extending the lifespan of your industrial cooling system is a blend of regular maintenance, operational efficiency, and smart upgrades. By implementing these tips with a specific focus on air-cooled chiller applications, you’ll save costs, improve efficiency, and ensure uninterrupted operations.